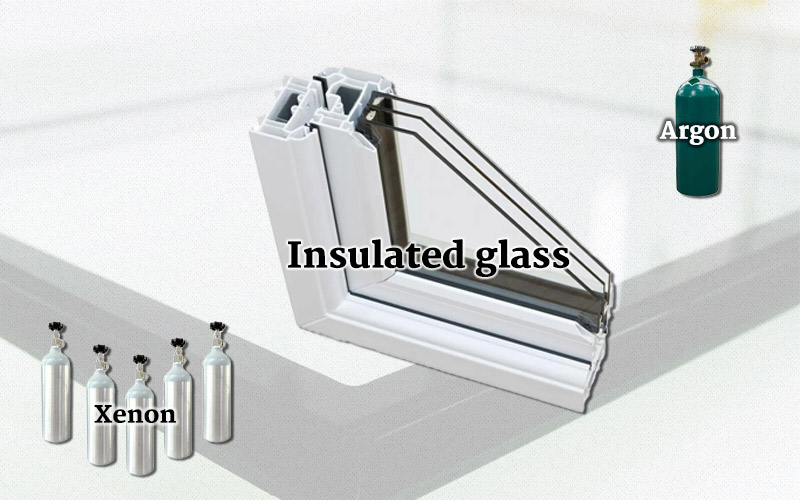
The insulated property of insulated glass has a strong relationship with the type and concentration of inert gas filled in it. Through the research on it, the use quality of inert gas in insulated glass can be improved.
Application of Inert Gas in Insulated Glass
Inflatable insulated glass is different from ordinary glass, mainly in the hollow space composed of two pieces of special glass into argon, xenon and other inert gas, and then use the composite binder with higher air tightness and strength to fill the gap of insulated glass, to avoid the leakage of inert gas.
Compared with ordinary double-layer glass, the sound insulation, heat insulation and practical beauty of inflatable insulated glass are more prominent. Generally, the higher the inert gas density in insulated glass is, the more significant the effect of improving internal heat convection and reducing heat loss is. Therefore, the inert gas concentration in insulated glass is an important index to detect the quality of insulated glass.
Thermal insulation is one of the most representative characteristics of inflatable insulated glass, and it is also a concrete manifestation of fully exerting the thermal conductivity of inert gas. If the thickness of the hollow cavity(air layer) increases, the thermal resistance of the window will increase accordingly. In general, the thickness of the hollow cavity of the insulated glass is suitable in the range of 12-18mm. If the hollow cavity itself is less than 12mm, the heat conduction of the glass will increase rapidly; if the thickness of the hollow cavity is greater than 18mm, there will be an air convection layer inside the glass, which will affect the energy-saving performance of the glass. Therefore, in order to ensure that the application performance of the insulated glass meets the energy-saving and use requirements, The thickness of the hollow cavity must be effectively controlled. In addition, by filling inert gas into the insulated glass can play a good protective effect, that is, the inert gas has lower thermal conductivity than air, which can effectively improve the insulation of the insulated glass. It can also be said that the inert gas in the hollow cavity is A key indicator that affects the insulation of insulated glass.
Therefore, when inert gas is applied in insulated glass, it is necessary to effectively control the thickness of the cavity, the type and filling amount of inert gas in insulated glass in combination with the requirements of thermal insulation and anti irritability of glass, so as to maximize the role of inert gas in insulated glass.
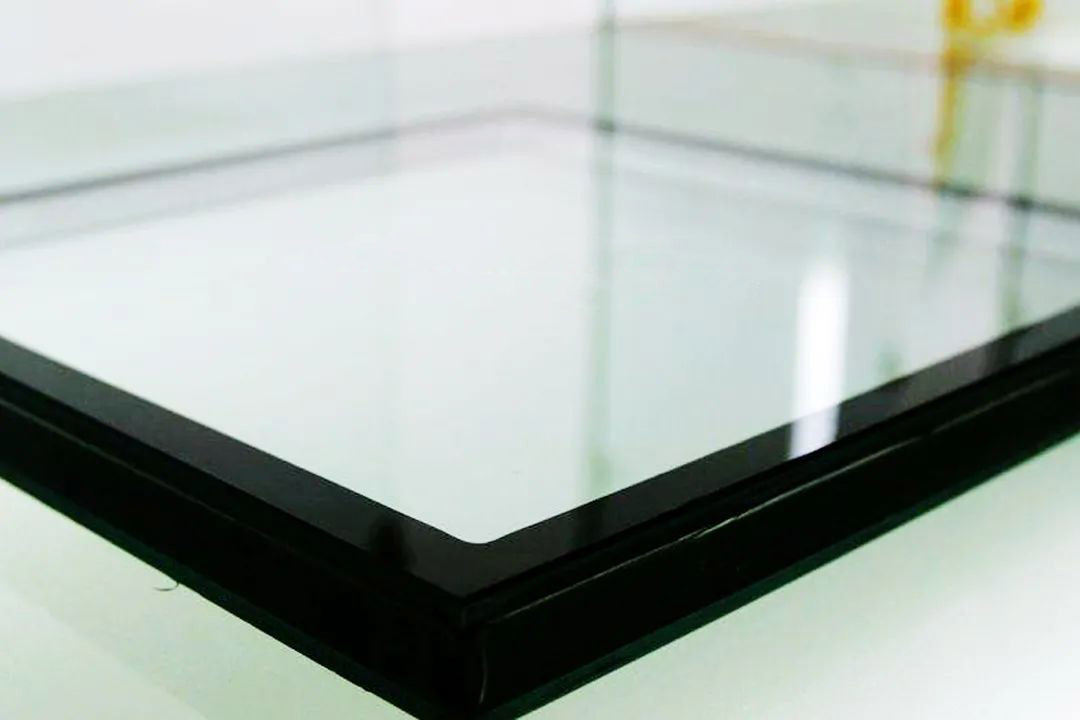
Quality Inspection Index of Inert Gas Application in Insulated Glass
1. Volume percentage of gas
In the evaluation of the application quality of inert gas in insulated glass, the volume percentage of gas is a very important index, and its value will have a great impact on the energy-saving effect(heat transfer efficiency) of insulated glass itself. The volume percentage of gas mainly refers to the proportion of inert gas in the mixed gas in the cavity of insulated glass. Taking argon as an example, the higher its concentration is, the smaller the thermal conductivity of insulated glass is, and the more remarkable the insulation effect is; In addition, inert gas can significantly improve the thermal conductivity of coated insulated glass. Therefore, in order to improve the thermal insulation and energy saving of insulated glass, the percentage content of inert gas in the mixed gas should be increased as much as possible, generally not less than 85%.
2. Gas leakage rate
This index mainly refers to the percentage of the total gas volume leaked out from the middle gas layer of insulated glass every year, which will have a great impact on the actual service life of insulated glass. Generally speaking, the lower the gas leakage rate, the longer the service life of insulated glass, so the gas leakage rate can be used as an important standard to evaluate the quality of insulated glass.
3. Gas seal durability
This index mainly refers to the percentage of gas volume of insulated glass under the action of climate cycle test, and generally its value should be no less than 80%, that is, the proportion of inert gas volume of insulated glass after climate cycle test is no less than 80%. Gas seal durability can reflect the service life and durability of insulated glass itself. However, this index is not very effective in evaluating the service life of insulated glass, and can not quantify the actual leakage of inert gas.
Quality Detection Method of Inert Gas Application in Insulated Glass
1. High voltage spark method
The principle of this method is that the high-pressure spark formed by the equipment passes through the middle gas layer, and the plasma containing inert gas molecules is activated to form radiation wave. Then, according to the theoretical knowledge of emission spectroscopy, the corresponding photons are collected and analyzed with the instrument, and the content of inert gas is calculated and determined finally. This method will not damage the samples of the insulated glass, which is a widely used nondestructive quality inspection method, which is suitable for the quality inspection of the insulated glass in use, the quality management of the inert gas filling stage in the production process and the consistency check after the glass installation. But this method has some limitations, such as when the insulated glass has double hollow cavity or the thickness of glass is too large, high-pressure spark can not activate the inert gas in the hollow cavity, so it is impossible to accurately determine the actual concentration of inert gas. Therefore, when using this method, it is generally necessary to ensure that the thickest laminated glass is within 10 mm and the thickness of the intermediate gas layer is 24mm.
2. Oxidative paramagnetic method
This detection method is based on the principle that the magnetic susceptibility of oxygen is several times higher than the magnetic susceptibility of the general gas. The oxygen content is determined by analyzing the magnetic susceptibility of the mixed gas, and then the actual content of the inert gas is determined by reverse calculation. In practical applications, it is necessary to destroy the tested insulated glass sample and take out the intermediate gas layer, and only the inert gas content can be measured, and the type of inert gas cannot be qualitatively analyzed. This detection method has the advantages of simple operation and high efficiency. It is mainly used in production lines or laboratories to quickly determine the performance of insulated glass, such as testing the durability and volume percentage of insulated glass gas seals.
3. Gas chromatography
Gas chromatography is mainly based on the basic principle of separation of mixed gases and the use of professional detectors to identify mixed gases. This detection method has the advantages of high separation and analysis efficiency, low consumption of analysis samples, and wide application range. The application sensitivity of this detection method can reach the μg level. It can not only determine the inert gas content, but also the leaked inert gas content, and is especially suitable for the measurement of gas leakage rate. However, this quality inspection method has higher requirements for the performance of the actual measuring instrument, so it is generally used in laboratory quality inspection.
Inflatable insulated glass is a kind of building material used more in modern architectural decoration, which will have a great impact on the durability and aesthetics of construction projects. Inert gas is a key factor affecting the performance of insulated glass. In actual applications, in addition to considering the basic design requirements and specifications, attention should also be paid to the flexible application of quality inspection methods such as gas chromatography and oxygen paramagnetism to insulated glass. Use performance testing to improve the quality of the inert gas in the insulated glass.