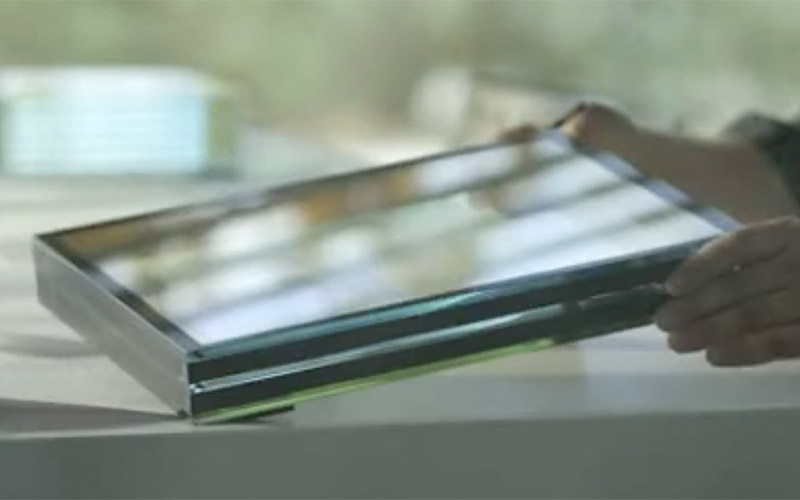
With the development of glass deep processing industry and people’s in-depth understanding of the performance of insulated glass, the application of insulated glass is expanding, and people’s requirements for the quality of insulated glass are higher and higher.This paper mainly describes the production process of insulated glass, the selection of materials and the quality control in the process.
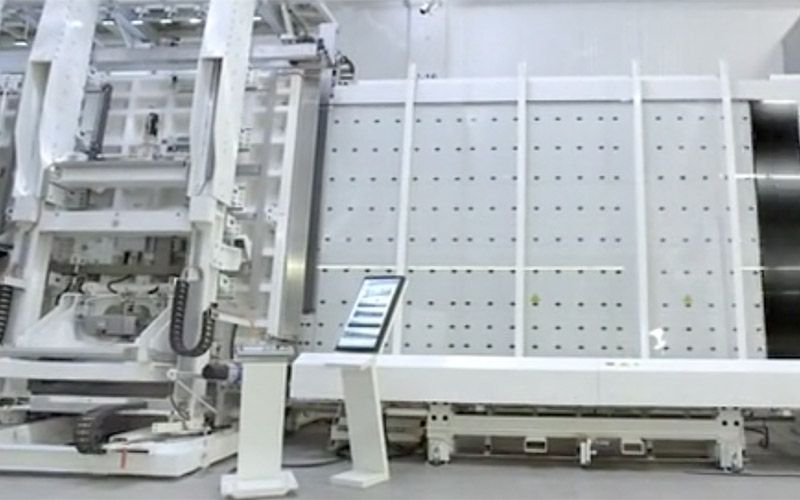
Classification and Technological Process of Insulated Glass
1. Classification of insulated glass
At present, there are two kinds of insulated glass on the market. One is double channel sealed insulated glass with aluminum groove, which has complex processing technology; The other is the rubber strip type insulated glass, the processing technology is relatively simple.
2. Production process
(1) Preparation of glass semi-finished products.
Glass cutting – pretreatment (including edge grinding, drilling, washing, tempering, sandwich, etc.) – matching tablets.
(2) Insulated glass products
Glass semi-finished products – washing (deionized water) – glass plate – placing aluminum frame – plate pressing – applying a second layer of sealant – curing – Inspection – warehousing.
Among them, the production process of aluminum frame is: cutting (automatic bending) aluminum strip – inserting angle – pouring molecular sieve – composite aluminum frame – applying butyl rubber (the first sealant).
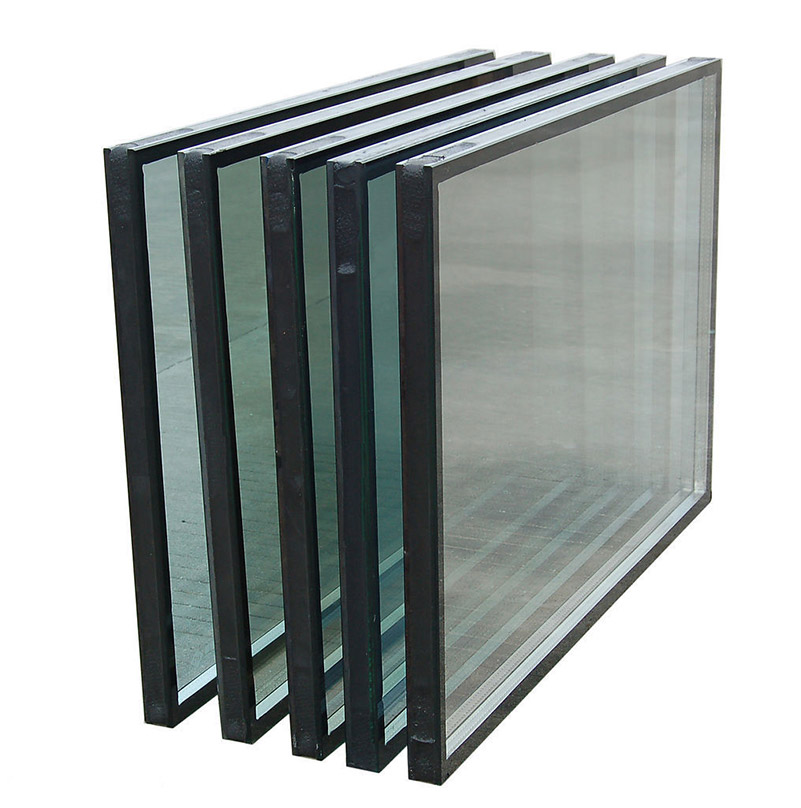
Material Selection of Insulated Glass
The main materials for producing insulated glass are: original glass, aluminum strip and insert angle, molecular sieve (desiccant), sealant (butyl rubber, polysulfide rubber, silicone structural rubber, etc.).
1. Selection of original glass
(1) The original glass used for insulated glass should be selected according to the functional requirements.The original glass for producing insulated glass can be float glass, coated glass, heat absorbing glass, tempered glass, laminated glass and fireproof glass.The quality and performance of the original glass should meet the current standards, and can be used after passing the inspection.Ordinary flat glass should be avoided because its transparency and strength can not meet the requirements.
(2) For different manufacturers, different batches of the original piece of glass before cutting should first check whether there is color difference, for large color difference of glass, should be used in different projects or different building facade.
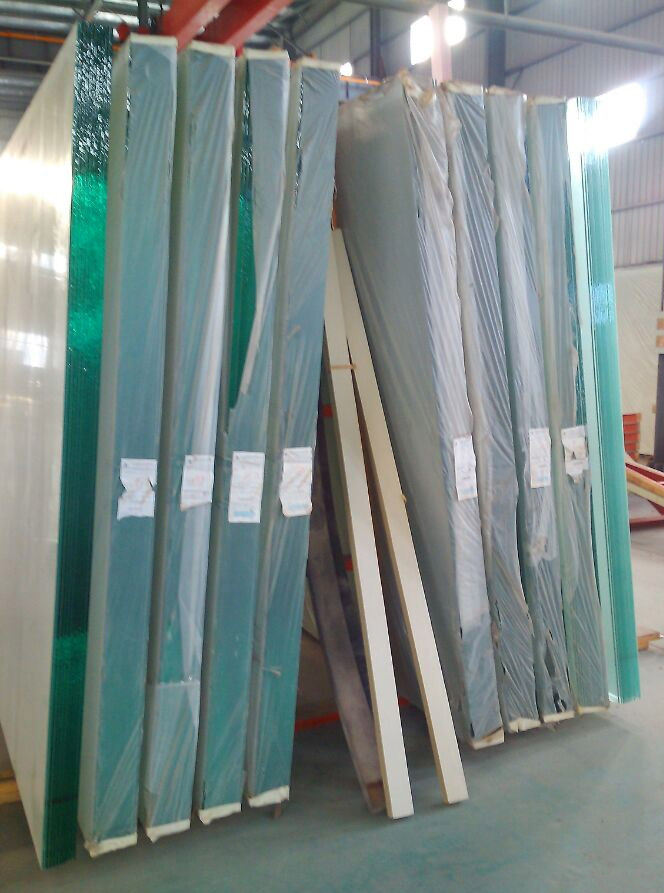
2. Selection of aluminum bar and angle
(1) The thickness of the aluminum bar shall be between 0.3-0.35mm, and the thickness shall be uniform. The aluminum bar spacing frame shall be straight and straight without distortion, and the surface shall be smooth and smooth without scratch, and heavy scratch is not allowed. The pores should be uniform and neat, all of them should be penetrated without burr, and there should be no leakage after filling molecular sieve with diameter of 0.5-0.85mm. There is no stain, spot or bad oxidation of flakes on the surface.
Aluminum strip must be anodized or decontaminated treatment. The surface oxide film is intact without falling off and mildew. If bending is required, products of good quality and high grade shall be selected to improve the utilization rate of aluminum strip.
3. Selection of molecular sieve (desiccant)
Molecular sieve (desiccant) with 3A pore diameter should be used in the production of insulated glass.The molecular sieve should be packed with plastic film to ensure that the molecular sieve is not affected by moisture.The particle size of molecular sieve should be uniform without powder. The particle diameter is 0.5-0.8mm, and the point contact crushing force is greater than or equal to 20n / particle. Before use, the activation performance of molecular sieve should be tested, that is, after 20g molecular sieve is added with 20ml water, the water temperature difference should reach above 30 ℃.
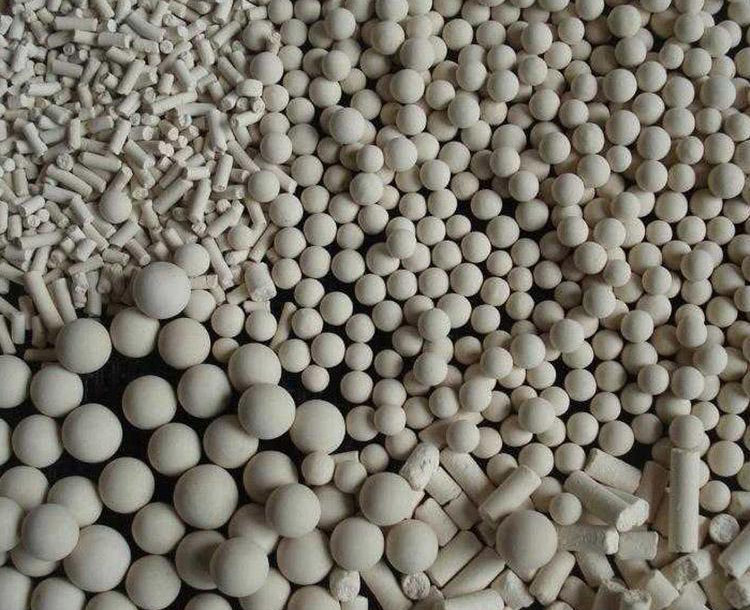
4. Selection of sealant
(1) Selection principle of sealant
In the production process of insulated glass, the density adhesive with good air tightness, UV aging resistance, high temperature and high humidity aging resistance, reasonable structural strength, easy operation and harmless to health should be selected.
(2) Selection of butyl rubber
Butyl rubber is the first sealant of aluminum strip insulated glass, which needs to meet the current industry standards.Butyl rubber is a kind of hot melt adhesive with low water vapor permeability (the lowest in insulated glass adhesive) and high viscosity. It is the most effective barrier between aluminum strip side and glass to block water vapor.Butyl rubber needs to be heated, pressed, extruded and coated on both sides of aluminum strip by special machine.At present, the heating temperature and pressure of butyl produced by various enterprises are different.According to the experience in actual production and use, it can be judged that Those low heating temperature, large amount of glue is produced during the process of sizing (when the rubber nozzle is at the same position) and easy to break, low bonding strength with aluminum strip and glass, and difficult to remove when sticking to aluminum strip or glass are not good butyl rubber.Therefore, in the selection of butyl rubber, not only pay attention to the quality, but also understand the use requirements of rubber.
(3) Selection of polysulfide glue
Polysulfide glue is the largest amount of sealant in the production process of insulated glass, which should meet the current industry standards.Polysulfide glue has good oil resistance, solubility resistance and sealing property. The use of polysulfide glue requires metal oxide as curing agent to polymerize it, and the distribution ratio of the two components is about 1:10. As the matching proportion and uniformity have little influence on the sealing effect, polysulfide glue can be applied by machine or by hand.Requirements for selection of polysulfide glue: clear color difference between two components, valid for more than half a year, strong UV resistance, good fluidity and curing elasticity. Therefore, polysulfide glue is also the preferred second sealant for insulated glass.
(4) Silicone structural sealant
The production of insulated glass used in structural installation should use neutral silicone structural sealant, which should meet the current industry standards.Silicone structural sealant has excellent structure, aging resistance and ultraviolet resistance, but its weakness is high water vapor permeability. Therefore, the silicone structural sealant is mainly suitable for places with strong light and poor environment, such as glass curtain wall, etc. at the same time, butyl rubber must be used as the first sealant.
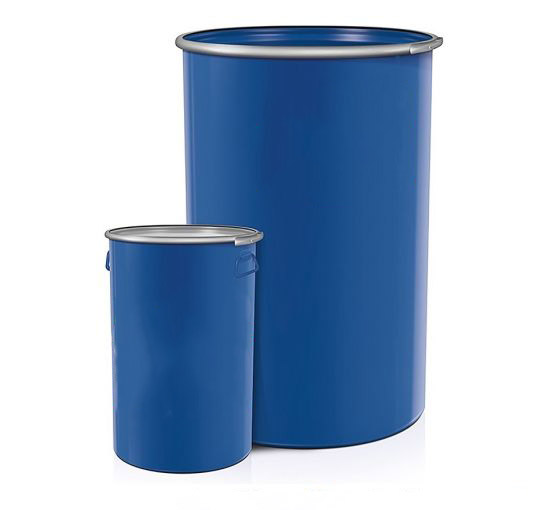
Quality Control of Insulated Glass
In order to ensure the quality of insulated glass products, insulated glass manufacturers should do well in the following aspects:
1. Better production process
A better insulated glass production process is an effective way to improve the quality of insulated glass.Good production process must have the following two elements. First, continuous production line. Only continuous production line can ensure the quality consistency of insulated glass products from original glass to qualified finished products; Second, whether it is the first seal or the second seal equipment, we should try to use a high degree of automation sealing equipment. Only in this way can we minimize the impact of human factors on product quality.
2. Perfect production environment
Insulated glass must be produced in an environment without dust, solvent pollution and suitable temperature. The dust pollution in the workshop will have a great adverse impact on the bonding effect of each component of insulated glass sealing system. Because of the existence of solvent, the adhesive force of butyl rubber will lose and the first seal will fail. Therefore, do not use volatile substances in the production workshop, and keep the air unobstructed. The suitable temperature is the necessary condition for the effective result of the two seals. The glue supply temperature of the second sealant should be above 10 ℃ as far as possible. Only the suitable temperature can make the sealant achieve the use effect within the specified time, such as the initial adhesive force, shear strength, elastic modulus and sealing performance.
3. Excellent production equipment
Excellent production equipment is the quality assurance of insulated glass products. The equipment and measuring tools for processing insulated glass shall meet the requirements of relevant regulations, and regular inspection and measurement certification shall be carried out to ensure the quality of processed products.Excellent production equipment is the quality assurance of insulated glass products. The equipment and measuring tools for processing insulated glass shall meet the requirements of relevant regulations, and regular inspection and measurement certification shall be carried out to ensure the quality of processed products. Such as the machining accuracy of the equipment, the accuracy of the pressure indicating device, the accuracy of the measuring tools, etc, Should be timely inspection, maintenance or measurement identification.
The basic equipment for insulated glass production includes cutting machine, edging machine, cleaning and drying machine, upper frame, laminating machine, tablet pressing machine, manual or automatic sealing machine, butyl rubber coater, deionized water production equipment, automatic air filling device, etc.
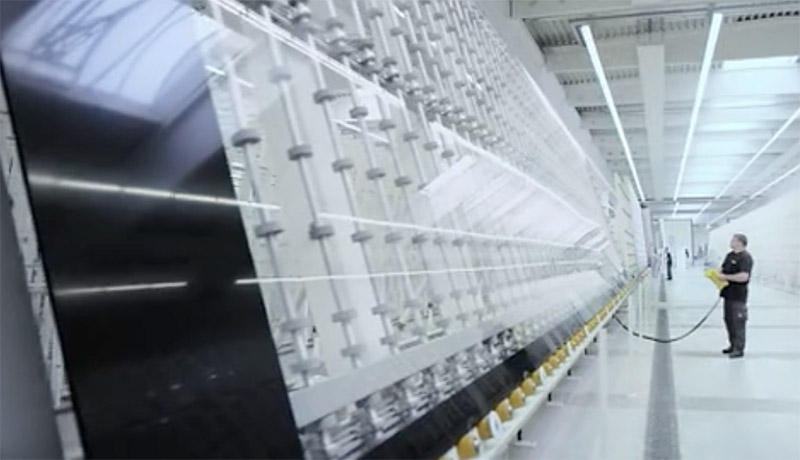
4. Qualified supporting materials
The selection of qualified supporting materials is a necessary condition for the production of qualified insulated glass. Without qualified supporting materials, it is impossible to produce high-performance insulated glass products. Therefore, insulated glass manufacturers must determine the qualified suppliers of main materials, strictly implement the provisions of 3C compulsory certification implementation rules for material suppliers, and ensure the inspection of incoming materials. If it is necessary to change the material manufacturer, the manufacturer must be required to provide material samples, and carry out necessary insulated glass products and inspection. At the same time, in the process of processing, the use of supporting materials should be tracked and inspected at any time.
5. Strict process control
(1) The cutting machine should use volatile and easy to clean cutting oil. When cutting, clean the table at any time to ensure that there is no glass slag on the table and the glass is not scratched.
(2) If the glass needs to be ground or tempered, it is necessary to ensure that the surface quality and flatness of the glass meet the standard requirements, especially the ground glass can not be placed for a long time, and it should be cleaned immediately.
(3) The drying air of insulated glass cleaning machine should be filtered. Deionized water should be used to clean the glass before lamination. No scratch, broken corner, water stain or residual water drop is allowed on the washed glass surface.
(4) Pay attention to check the appearance quality of the glass in the last film, and the unqualified ones can not be used. In addition, when processing the coated glass, pay attention to the position of the film surface, and do not make mistakes. When processing directional insulated glass, the drawings should be carefully checked to avoid wrong combination.
(5) The upper spacer frame should be accurately positioned, especially when processing multi-layer or table type insulated glass, it is necessary to carefully look at the drawings to ensure that the sealing amount meets the requirements.
(6) When laminating, the pressure of the tablet press should be uniform, so that two or more pieces of glass are bonded together with the aluminum spacer strip by butyl rubber, and the butyl rubber is evenly spread on the spacer strip to form the first seal.
(7) The second sealant of insulated glass should use two-component sealant beater. The gluing machine should be equipped with a and B component glue supply pressure indicator, the glue output pressure can be continuously adjusted, evenly injected into the glass sealing area, and the two sides of the spacer frame should be fully filled. The two-component sealant beater shall be equipped with independent control valve to facilitate glue discharge and glue gun cleaning. Butterfly test shall be conducted before sealing operation to check the mixing uniformity of two-component sealant. During the sealing process, the filling amount of the second sealant should be observed at any time to ensure that the sealant fully contacts with butyl rubber and is flush with the glass edge. There should be no air passage and bubbles in the middle, and the glue depth should meet the requirements.
(8) The air filling of insulated glass can adopt automatic air filling device, and the air filling amount shall not be less than 85%.
(9) The size of the aluminum strip shall be accurately cut according to the type of the second sealant to ensure that the sealing amount meets the standard requirements.
(10) The butyl rubber coater should be able to ensure that the glue is uniform, without leakage and continuous glue, and evenly coated on the aluminum strip. The width of butyl rubber should not be less than 3mm, the thickness should be controlled within the range of 0.3-0.5mm when laminating, and the corner of aluminum frame must be sealed with butyl rubber. If it is bending aluminum bar, molecular sieve filling hole must be sealed with butyl rubber.
(11) Before pouring the molecular sieve, we must check whether the molecular sieve is effective. The simplest way is to lick the molecular sieve with the tongue to see if the tongue has the feeling of fever. The aluminum frame filled with molecular sieve should be used to synthesize the middle hollow in 45 minutes.
(12) When the off-line low radiation coating glass is processed to make hollow glass, the film must be removed in the sealing area at the side.
(13) After the opening of the point supported insulated glass, the opening must be sealed with double seals.
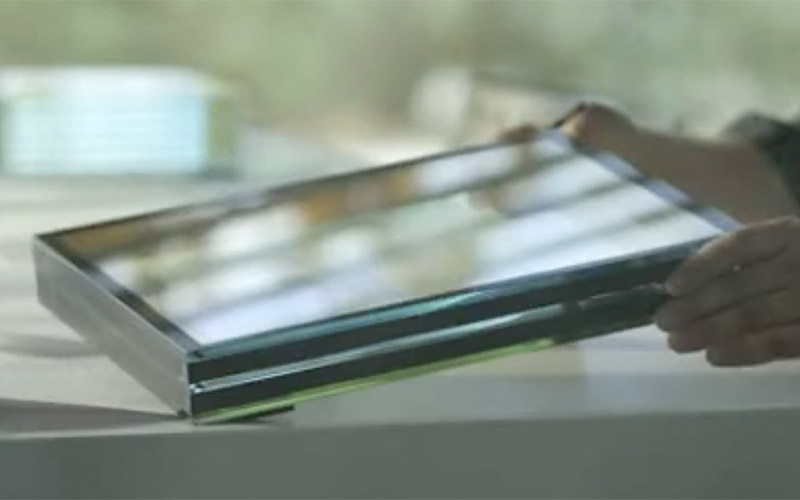
In a word , to produce high-quality insulated glass products, we should not only have advanced technology, excellent equipment and perfect environment, but also choose high-quality raw materials, strictly abide by the production process regulations of insulated glass in the process of processing, and effectively control the process.