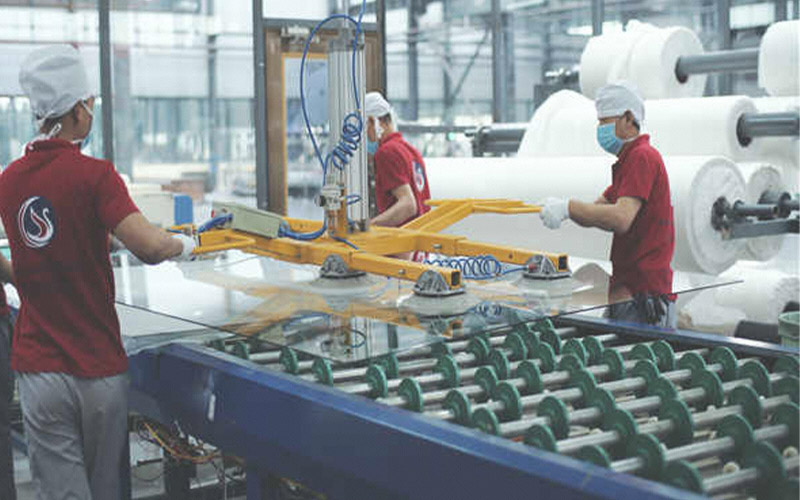
Insulated glass is a complex system with a large number of raw materials and complicated production process. In order to produce a piece of qualified insulated glass, it is necessary not only to have high-quality raw and auxiliary materials, but also to carry out self inspection and mutual inspection between each process. In the production process, the environment should be controlled and the operation of employees should comply with the regulations. Through the analysis of the unqualified items of insulated glass, most of the reasons for the unqualified items are related to the poor quality of raw and auxiliary materials, unskilled equipment operation and not operating according to the regulations.
Common Causes of Non Conformity
1. The width of adhesive layer does not meet the requirements
The reasons why the width of adhesive layer does not meet the requirements are as follows:
(1) The glue machine is not maintained on time or the pipeline is blocked, the glue speed and the amount of glue are unstable, and there is short glue during the glue glue process.
(2) The operator did not operate in strict accordance with the operating procedures, and did not repair the bending part of the spacer bar.
(3) The unskilled operation of the spacer bar bending machine makes the bending part of the spacer bar bulge seriously.
(4) Manufacturers do not understand the insulated glass production process or weak quality awareness, do not understand the impact of insufficient adhesive layer thickness on product quality.
(5) In order to save cost, the production enterprises reduce the amount of glue, so that the width of hollow glass sealant can not meet the standard requirements.
For the width inspection items of the inner sealant, some companies have no problems with the factory inspection, but the third-party authority fails to pass the inspection. The reason may be that the company did not measure at the narrowest point during the factory inspection. The width of the inner sealant should be in the butyl Measure the narrowest part of the glue, and measure the width of the outer sealant from the junction of the inner sealant and the outer sealant to the narrowest part of the outer edge of the outer sealant.
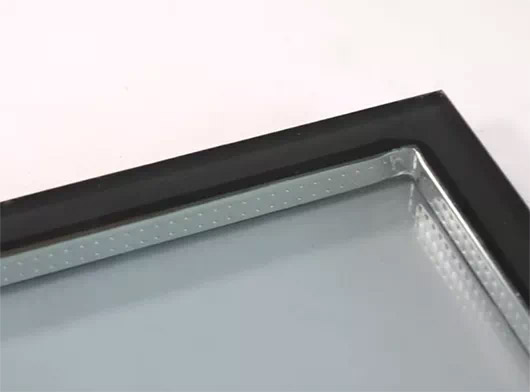
2. The inner sealant is uneven and continuous
The heating temperature of butyl rubber coater does not reach the tapping temperature, the uneven and discontinuous discharge of butyl rubber coater, and the unskilled coating operation of operators may lead to uneven and continuous inner sealant.
3. Sealant flowing
When the silicone rubber used for insulated glass contains white oil, the white oil will react with butyl rubber and melt, resulting in sealant flowing.
4. The amount of desiccant dust in the spacer strip is unqualified
When the amount of desiccant dust in the insulated glass spacer strip is unqualified, the dust will fall off, resulting in stains on the inner surface of the glass, affecting the quality and appearance of the insulated glass.
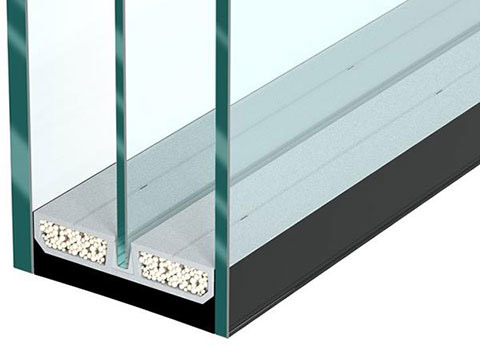
5. Unqualified dew point
At dew point temperature, the condensed water floating in the air is called fog, and when it sticks to the solid surface, it is called dew. The lower the dew point, the drier the air in the cavity. The dew point of insulated glass should be less than -40℃.
The reasons for unqualified dew point inspection are as follows:
(1) The reason of desiccant quality. When the moisture content in the hollow cavity is high, there is still excess moisture in the hollow cavity after the desiccant is saturated.
(2) Personnel reasons. When the size of desiccant selected by the enterprise is small, the desiccant will be adsorbed on the inner wall of the pipeline by the generated static electricity during the filling process, resulting in the desiccant in the filling interval less than the specified value, resulting in insufficient desiccant water adsorption capacity; The pipeline is blocked because the filling machine is not cleaned regularly. In the set time, the desiccant filled into the interval bar is less than the specified value, resulting in the insufficient moisture adsorption capacity of the desiccant.
(3) Environmental reasons. The relative humidity control of desiccant filling environment is not strict, which leads to the high relative humidity of the environment, and the desiccant has been saturated before lamination, so it can not work.
(4) Management reasons. The desiccant after opening was not sealed after filling, resulting in the decrease of residual adsorption capacity of desiccant; The desiccant was not used up within the specified time after unsealing.
(5) The reason for the quality of the spacer strip. The gas permeability of the pores on the spacer strip is not enough. If the pores on the spacer strip are not permeable, it means that the excess water vapor in the hollow cavity will not be absorbed by the desiccant through the pores.
6. The durability of water gas seal is unqualified
The following reasons may lead to the disqualification of the water gas seal durability test:
(1) Raw materials. The elastic sealant is aging and its performance does not meet the requirements. During the water-gas seal durability test, due to excessive stretching and compression, the sealant loses its elastic contraction function, causing excessive moisture to enter the cavity through the edge of the hollow glass; in all elastic sealants, silicone The amount of glue used is the largest. When silicone sealant is used as an external sealant, since silicone oil is mixed into the silicone glue, the silicone oil may ooze out during the test and cause the adhesive performance of the external or internal glue to decrease.
(2) Technology and equipment. The correct temperature is generally 10~35℃, and the thickness of the adhesive layer should be met. If the mixing ratio is not set in strict accordance with the weight ratio or volume ratio specified by the sealant manufacturer, the application period and curing time of the sealant will be affected.
(3) Personnel. Before applying the outer sealant, the operator did not carry out the “Butterfly” test and used the outer sealant mixed unevenly; The operator moved the partially solidified insulated glass; The operator did not operate according to the regulations, so that the width of the outer sealant and the inner sealant did not meet the requirements; The original piece of glass is not cleaned or there is dust on the spacing strip, which makes the bonding between the spacing strip, the original piece of glass and the inner seal not firm; Failure to carry out factory inspection on the purchased outer and inner sealants as required, so that unqualified sealants enter the production process.
Influence of Unqualified Items
Spacer, desiccant, sealant (or composite material) and glass form the edge sealing system of insulated glass. The quality of edge sealing system determines the service life of insulated glass. If there is visible water vapor in the hollow cavity of the insulated glass, it is the failure of the insulated glass. The service life of insulated glass is terminated after failure.
The sealing performance and structural stability of insulated glass depend on the elastic sealant, which is also called the second sealant. The second sealant binds the glass and the spacer strip into a rigid but flexible system, and transfers the external load from the outer glass plate to the inner glass plate of insulated glass. In the insulated glass sealing system, the bad adhesion of any combination of sealants will have an adverse effect on the function of insulated glass, and even fail in serious cases.
Butyl glue is the inner sealant of insulated glass, also known as the first sealant. Among all insulated glass sealing materials, butyl glue has the lowest permeability index, only 1/15~1/20 of that of elastic sealant. It is an important barrier to prevent external water vapor from entering into the hollow cavity of insulated glass. If the width of butyl glue is unqualified or there is fracture, water vapor will quickly enter into the hollow cavity through the fracture position, It directly leads to the failure of insulated glass.
The unqualified dew point and moisture seal durability of the insulated glass means that the insulated glass has failed and needs to be removed and replaced with a new glass. If the insulated glass is used as a curtain wall, the risk of the outer glass falling off is increased.
Insulate d glass is a whole made of many kinds of materials. Because the dry gas is sealed in the hollow cavity, the heat transfer coefficient is reduced, so it has good energy saving and heat insulation performance. In order to keep the gas in the hollow cavity continuously dry, the edge sealing system plays an important role. Most of the unqualified items of insulated glass are related to the edge sealing system.