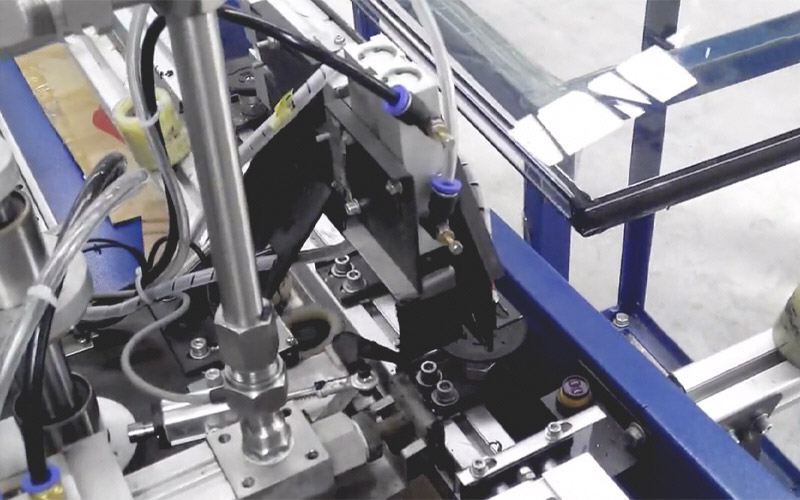
As the most widely used safety and energy-saving glass product, insulated glass is widely used in the construction industry due to its good safety, energy-saving, sound insulation and anti-condensation properties. The composition of insulated glass involves glass, sealant and desiccant, among which the sealing and bonding performance mainly depends on sealant. How to select sealant that meets the requirements is of great significance to the quality assurance of insulated glass.
Sealant Classification and Characteristics
The main types of sealants used in insulated glass are butyl rubber, polysulfide rubber, silicone rubber and polyurethane sealant. At present, the production process of insulated glass is mainly based on double sealing. In the process of double sealing, butyl rubber is used for the first sealing, and its gas permeability and water vapor permeability are the smallest, which mainly prevent water vapor permeation. The second sealing uses polysulfide sealant, silicone sealant or polyurethane sealant. Polysulfide sealant or silicone sealant has better adhesion performance. The main function is adhesion performance, and it also plays a role in auxiliary sealing. Polyurethane glue is also used as a secondary sealant, but the amount is small.
Compared with silicone rubber, polysulfide rubber has better oil resistance, solubility, sealing property and better stability. It is not easy to incompatible with glass, butyl rubber, desiccant and aluminium strip. It is an ideal sealing material for insulated glass. Silicone glue easily reacts with other materials and affects the product quality and service life of insulated glass. However, silicone glue has become the main material for insulated glass sealing due to its excellent adhesion, aging resistance and UV resistance. At present, the second sealant used in the market is mainly polysulfide and silicone rubber. Because of the high price of polysulfide, it has a strong pungent odor during use, which is difficult for many production operators to accept and unwilling. In terms of cost reduction, companies also tend to choose silicone glue, which makes the use of silicone glue obviously dominate.
Silicone Sealant Quality Requirements
In comparison, silicone rubber has structural properties, aging resistance and UV resistance, and is more adaptable to the environment, but its weakness is its high water vapor transmission rate.
Through experiments on the performance of insulated glass exposed to atmospheric exposure, under the same conditions: polysulfide type samples exposed to 3 years, the mass of water penetration was 0.35g, 5 years was 0.55g, and silicone type samples exposed to 3 years of water penetration 0.8g. The type of outer sealant is a significant factor affecting the permeability of insulated glass. The water permeability index of insulated glass bonded by silicone sealant is much higher than that of polysulfide glue, and the difference in durability of the two is nearly doubled. Silicone glue has advantages in price and bonding performance, but its high water vapor transmission rate is its main problem. The use of silicone glue as a sealing material for insulated glass requires the quality of the sealant to meet the requirements.
Generally speaking, the quality of silicone sealant should have good adhesion, certain elasticity and elastic recovery ability, good anti-ultraviolet aging performance, low water vapor permeability, and no impurities after the sealant construction, and it is convenient for production, operation and construction. , And at the same time ensure the compatibility of sealant, butyl rubber, desiccant and other materials.
The Quality of Silicone Sealant
Silicone sealants are usually high-molecular polymers, mainly based on hydroxyl-terminated polysiloxane as the matrix material, composed of vulcanizing agents, catalysts, plasticizers, reinforcing fillers and other auxiliary agents. Good quality silicone adhesives, The matrix material needs to reach the proportion of corresponding requirements. In the sealant market, competition is fierce. In order to reduce costs, some manufacturers use fillers instead of matrix materials. As a result, the quality of sealants cannot meet the requirements, resulting in decreased adhesion, poor elasticity, poor sealing performance, and poor weather resistance. , Which seriously affects the quality of insulated glass products. Especially when a large amount of cheap white oil is used instead of dimethyl silicone oil as a plasticizer, it may dissolve the butyl rubber, causing the insulated glass sealant to flow. This phenomenon may occur several days after the production of the insulated glass. As soon as it appears, the butyl rubber seal fails or is affected, and the quality problems of insulated glass products will also occur. Now there are even a few manufacturers that can produce different quality sealants according to customer price requirements. The production process control is chaotic and the quality is difficult to guarantee.
Silicone sealant is the main raw material for the production of insulated glass, and its quality has a greater impact on the quality of insulated glass products. Manufacturers of insulated glass should choose to use sealants that meet the production requirements, and at the same time control the production process to ensure that the insulated glass products quality.